“ULTIMATE SEAL” SKIRT LINER – NO MORE GROOVES IN YOUR CONVEYOR BELT
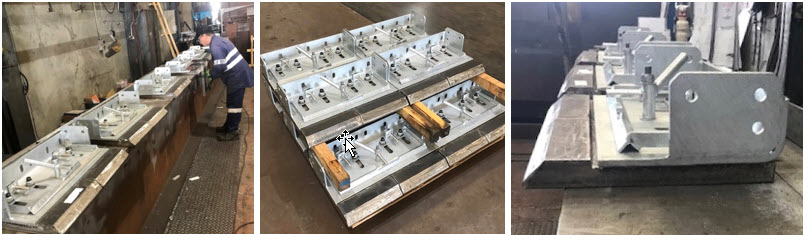
Conveyor skirting system design faces the challenge of forming a seal between the carry belt and skirt liner for the containment of material and dust without creating excessive friction wear to the carry belt itself. H & B’s latest innovation in conveyor skirts, the “Ultimate Seal” skirt design was developed with this in mind.
Ninety nine percent of skirt designs have a gap between the primary seal (skirt liner) and the secondary seal (skirt rubber). Traditional conveyor skirt design comprises of the skirt rubber and skirt liner attached either side of the skirt panel; between which a gap exists. This gap is inevitably a trap for rogue material and dust to collect in and eventually form a hard interface which can rub continuously against the belt forming a groove, ultimately damaging the belt. H & B Mining’s “ULTIMATE SEAL” skirt design is a step forward in providing the best possible sealing arrangement, while affording the best belt protection.
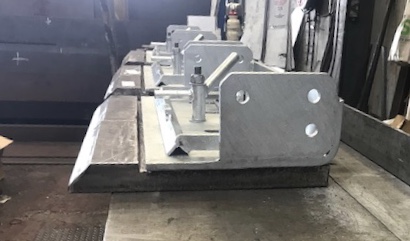
The “Ultimate Seal” conveyor skirt design eliminates the gap by changing the external shape of the skirt liner to interface with the skirt rubber. The improved liner-rubber interface closes the gap and denies the opportunity for material to gather and form a hard surface, protecting the belt from damage.
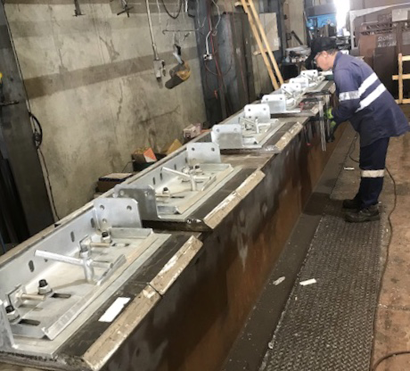
Thus far, the design has been installed at two mine sites in Western Australia’s Pilbara and has been a success. The future looks bright for yet another innovative design provided by H & B Mining.
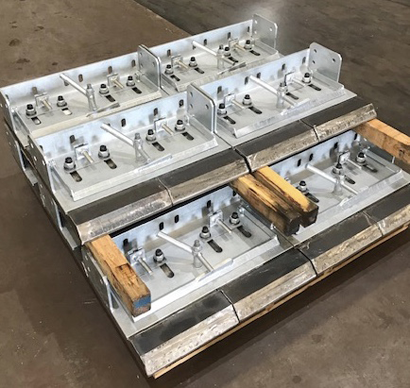
H & B Mining continually strives to develop new, safe and resource saving products. Our conveyor skirting solutions evolve according to challenges presented to us during conveyor transfer upgrades. Call (08) 9403 2993 to discuss conveyor design solutions with us.
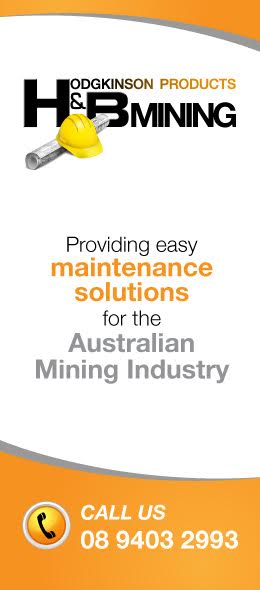
Latest News
WORKSHOP
7 41 Division Street,Welshpool,
Perth, Western Australia 6106
- Tel: 08 9403 2993
- info@handbmining.com.au
HEAD OFFICE
7 Tahiti Lane, Hillarys, Perth, Western Australia 6025
- Tel: 08 9403 2993
- info@handbmining.com.au